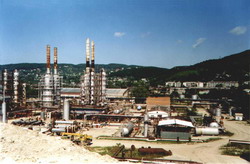
Порушення матеріального балансу при відборі фракції або теплового режиму в колоні може привести до небажаних змін фракційного складу продуктів - зміни температур початку або кінця кипіння фракції, що не відповідає вимогам на готову продукцію.
Процес ректифікації ведеться відповідно до кривої рівноваги залежно тиску насичених парів і температури кипіння фракції. Тому при зміні тиску в колоні необхідно коригувати температурний режим, щоб фракційний склад відбираються продуктів залишався незмінним. На жаль, оперативний персонал не в змозі в розумі обчислювати для кожного продукту, відповідно до кривої рівноваги, температуру відбору при зміні тиску в колоні. Тому при відносно стабільному режимі несподівано відбувається відхилення якості продукту від заданих показників. Так зниження тиску в колоні К-2 на 0,1 кг / см2 при незмінній температурі верху може привести до підвищення температури кінця кипіння бензину на 7-8 оС [ 1 ]. Такі коливання тиску в колоні є звичайними при зміні доби, вони незначні, і оператори зазвичай не коригують температурний режим в колоні. А так як лабораторні аналізи продуктів виконуються раз на 4 години, то багато відхилень в період між аналізами залишаються як би невидимими. Однак це не означає, що вони не позначаються на роботі, наприклад, реакторного блоку риформінгу або на якості готової продукції в товарному парку.
Тому при створенні НПФ «КОЛО» системи управління на установці первинної переробки нафти АТ-1 на ВАТ «НК Роснефть» - Туапсинський НПЗ »було поставлено завдання: підвищення стабільності ведення технологічного режиму установки в цілому і розрахунок параметрів раціонального режиму технологічного процесу в колоні К- 2.
Підвищення стабільності технологічного процесу - це відтворюваність заданого технологічного режиму з зміни в зміну, що вже гарантує стабільність якості продуктів. Якщо підібрати технологічний режим, який забезпечує певну якість продуктів, і порівняти його з поточним режимом через кілька днів, то можна помітити, що в режимах є певна різниця. Незначні щоденні зміни за окремими параметрами, на які оператори не звертають уваги, накопичуються і в сумі вже дають значні відхилення.
Наростаючий кому сукупних відхилень несподівано для операторів, при відсутності будь-яких видимих передумов з боку технологічного процесу, виливається в нібито «неякісний» лабораторний аналіз будь-якого продукту [ 2 ]. Перша реакція - «помилка лабораторії», так як процес йде «як по нитці», і мало у кого вистачає бажання проаналізувати кілька десятків параметрів за кілька діб і дати більш об'єктивне пояснення за даним фактом.
Тому першим завданням, яке необхідно вирішити, стало надання операторам технологічної установки засобів оперативної оцінки відхилення технологічного режиму від заданого в будь-який момент. Для цього процес первинної переробки нафти був умовно розділений на ряд ділянок:
- підготовка нафти;
- стабілізація нафти в колоні К-1;
- поділ на фракції в колонах К-2,4;
- печі.
При сталому режимі і задовільному якості продуктів начальник установки або технолог спеціальної командою з використанням пароля включає підсистему діагностики технологічного процесу, яка запам'ятовує поточний режим як «хороший», і потім починає розраховувати сукупний показник відхилення по установці в цілому і по кожній ділянці. Тепер оператор постійно тримає величину відхилення від заданого режиму під контролем, швидко визначає, на якій ділянці відхилення, за якими параметрами і, не вдаючись у довгі роздуми, просто повертає параметр до заданого «хорошого» значенням.
При випробуванні цієї підсистеми оператори не були введені в курс її роботи. Показники відхилення по ділянках і по установці, в цілому, коливалися в дуже значних межах навіть протягом однієї зміни. Після введення підсистеми в роботу і інструктажу операторів, коливання показників відхилень від заданого режиму різко скоротилися і стали складати не більше 20%. Нарешті, технологи домоглися щоденного відтворення заданого технологічного режиму. ( Рис.1 Структура системи раціонального управління установкою первинної переробки нафти )
Підсистема діагностики технологічного процесу стала основою для функціонування наступного завдання - розрахунку параметрів оптимального режиму технологічного процесу в колоні К-2. Підсистема реалізує наступні завдання:
- розрахунок відбору світлих нафтопродуктів з нафти;
- розрахунок температури верху колони і температури відбору гасу в залежності від тиску в колоні;
- розрахунок прогнозованої середньої температури кипіння бензину, температури початку і кінця кипіння гасу при поточному режимі в колоні;
- розрахунок кількості гострого зрошення в колону К-2;
- розрахунок кількості гасового циркуляційного зрошення;
- розрахунок пара в гасовий і дизельний стріппінг.
Рис.1 Структура системи раціонального управління установкою первинної переробки нафти
Розрахунок необхідної температури верху колони К-2 і температури відбору гасу, в залежності від тиску в колоні, прогнозованої середньої температури кипіння бензину, температури початку і кінця кипіння гасу при фактичному режимі в колоні К-2 дозволяють оператору визначити - який режим в колоні треба підтримувати , щоб якість бензину і гасу було незмінним, а також контролювати, в який бік і наскільки відбувається полегшення або ускладнення фракцій при дотриманні поточного режиму. Ці завдання працюють на основі кривих рівноваги для кожного продукту [ 3 ]. Розрахунок кривої рівноваги проводиться автоматично в реальному масштабі часу. При сталому режимі і стабільній якості продуктів відбираються проби на лабораторний аналіз бензину і гасу, при цьому фіксуються показники технологічного режиму в колоні К-2. Потім показники якості продуктів і режимні параметри заносяться в спеціальну таблицю, і система управління автоматично розраховує калібрувальні криві рівноваги для кожного продукту. Калібрування проводиться начальником установки або технологом один раз і повторюється при необхідності, наприклад, при зміні вимог до фракційного складу відбираються продуктів.Розрахунок кількості верхнього гострого зрошення колони К-2 і гасового циркуляційного зрошення виконується в залежності від кількості відбираються продуктів і вимог до чіткості поділу продуктів. Розглянемо це більш детально на прикладі роботи секції колони, що відповідає за розподіл бензину і гасу. Ця секція знаходиться між верхом колони і тарілкою відбору гасу. Секція містить 13 тарілок і служить для відділення від бензину гасової фракції. Як зазначено в літературі [ 1 ], Чіткість ректифікації залежить від флегмового числа, числа тарілок в секції, виходу ректифікату, ефективності та конструкції тарілок. Чіткість ректифікації характеризується «налягання» температур кипіння поділюваних фракцій і побічно може характеризуватися твором Y * N, де Y - флегмовое число для даної секції, N - число тарілок в секції. Задовільна чіткість поділу фракцій досягається при Y * N ~ 25 ÷ 50 і підбирається на працюючій колоні практичним шляхом, в залежності від конструктивних особливостей колони і ефективності роботи тарілок. Для бензинової секції твір Y * N було визначено рівним N1. Відповідно до цього коефіцієнтом, система автоматично розраховує необхідну кількість верхнього гострого зрошення.
Аналогічно для гасової секції твір Y * N було визначено рівним N2. Відповідно до цього коефіцієнтом, система автоматично розраховувала необхідну кількість гасового циркуляційного зрошення.
Розрахунок кількості пара в гасовий і дизельний стріппінг. Відповідно до рекомендацій [ 4 ], Були підібрані коефіцієнти, які дозволяють постійно розраховувати кількість пара в стріппінг в залежності від кількості одержуваного продукту і збільшення температури початку кипіння продукту в стріппінг на 12 ÷ 15 оС.
Впровадження завдань діагностики технологічного процесу і розрахунку раціонального режиму було здійснено НПФ «КОЛО» в складі АСУ ТП, створеної на базі ПТК «КОЛО-2000», однак прийняті технічні рішення можуть бути реалізовані практично в будь-якій сучасній системі управління.
Функціонування підсистем діагностики технологічного режиму і розрахунку раціонального режиму по колоні К-2 дозволило:
- зробити технологічний режим установки відтвореним від зміни до зміни;
- зробити протікання процесу ректифікації в колоні К-2 більш зрозумілим і «прозорим» для технологічного персоналу;
- оперативно інформувати технологічний персонал про необхідні дії при веденні технологічного режиму установки;
- стабілізувати коливання температури кінця кипіння бензину в межах 2 ÷ 3 оС;
- скоротити «налягання» температур кипіння бензинової і гасової фракцій до величини - не більше 5oС.
- 1. Мановян А.К. «Про чіткості погоноразделенія при перегонці нафти», Праці Грозного, випуск XXII, Технологія переробки нафти і газу. Виробництво палив, 1968р.
- 2. Слободкін В.М. «Ректификация. Побічні ефекти традиційних керуючих впливів ». Промислові АСУ та контролери, №11 1999р.
- 3. Лісіцин Н.В. «Оптимізація нафтопереробного виробництва», Хіміздат, Санкт-Петербург, 2003р.
- 4. Мановян А.К. та ін. «Про роботу отпарную секцій атмосферної колони з введенням водяної пари», праці Грозного, випуск XXII, Технологія переробки нафти і газу. Виробництво палив, 1968р.